Robotit ja konenäkö apuna elektrolyysiprosessissa
TEKSTI: THOMAS FREUNDLICH KUVA: PÄIVI KARJALAINEN
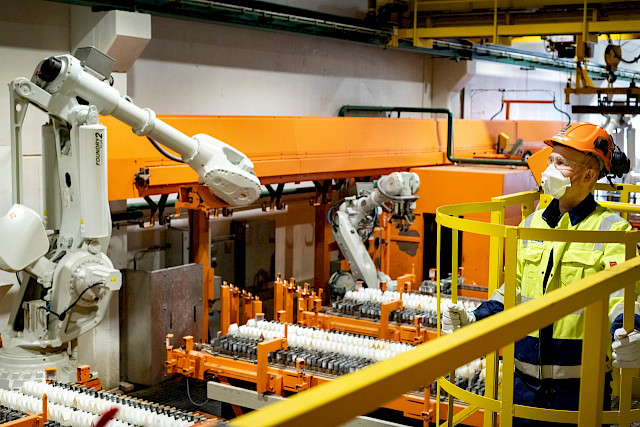
Bolidenin Kokkolan tehdas automatisoi sinkin valmistusta Algol Technicsin ja ABB:n ratkaisuilla.
Suomen länsirannikolla sijaitseva Boliden Kokkola on Euroopan toiseksi suurin sinkkitehdas. Tehtaan valikoimassa on noin 40 erilaista sinkkituotetta, joista osa on puhdasta sinkkiä ja osa puolestaan eri asiakkaiden tarpeisiin räätälöityjä seostuotteita. Tehtaalla tuotettua sinkkiä käytetään esimerkiksi autoihin, siltoihin, paristoihin, valopylväisiin ja rakentamiseen. Kokkolan tehdas edustaa sekä päästöjen pienuuden että energiatehokkuuden näkökulmasta alansa huippuluokkaa maailmassa.
Sinkkituotteiden valmistuksessa käytetään elektrolyysiprosessia, jossa elektrolyyttialtaisiin upotetut elektrodit saostavat sähkövirralla sinkkiä elektrolyyttiliuoksesta alumiinikatodin pinnalle. Prosessin aikana lyijystä valmistetut anodilevyt saostavat pinnalleen epäpuhtauksia elektrolyytistä ja kuluvat hieman, minkä vuoksi anodilevyt pitää puhdistaa ja niiden kunto tarkistaa säännöllisesti. Boliden Kokkolan AK2- tuotantolinjalla aiemmin osin käsityönä tehty prosessi on nyt pystytty automatisoimaan robottien sekä edistyksellisen 3D-konenäkösovelluksen avulla.
Elektrolyysin kuljetusjärjestelmällä tuodaan linjalle tyypillisesti 630 tai 720 anodia kerrallaan kunnostettavaksi. Anodit siirretään 45 kappaleen ryhminä. Robottien ja konenäköjärjestelmän avulla anodilevyt puhdistetaan, tarkastetaan ja huolletaan. Konenäkö tutkii usealla kameralla levyjen kunnon, ja niiden kuluneisuudesta riippuen palauttaa levyn prosessiin, lähettää sen kunnostettavaksi tai vaihtaa tilalle uuden levyn. Anodilevyjen kunnon lisäksi järjestelmä tarkastaa levyjen välissä olevat eristekappaleet ja tarvittaessa vaihtaa ne automaattisesti. Ennen konenäköasemaa kaikki levyt pestään sekä oikaistaan mekaanisella puristimella.
Turvallisuutta ja luotettavuutta
Järjestelmän toteutuksesta vastaava Algol on aiemmin toimittanut Bolidenin Kokkolan tehtaalle laajalti erilaisia tuotantojärjestelmiä.
”Boliden oli tehnyt paljon pohjatyötä elektrolyysiprosessin automatisoimiseksi”, kertoo myyntijohtaja Teemu Rantala Algol Technicsilta.
”Jo projektin alkuvaiheessa meillä oli selkeä tieto siitä, mitä anodilevyjen käsittely edellyttää, ja miten ratkaisu saataisiin päivitettyä osaksi tehtaan olemassa olevaa tuotantolinjaa. Levyjen käsittely hoidettiin aiemmin osin manuaalisesti Algolin toimittamilla nostureilla, joten ratkaisun automatisointi onnistui varsin luontevasti.”
AK2-linjan vanha laitteisto koostui automatisoiduista kuljettimista, pesuasemasta, varastopaikoista ja nosturista. Anodien kunnon tarkastus ja mahdollinen eristimien vaihto tehtiin manuaalisesti. Työ tehtiin liukuhihnatyyppisesti aivan laitteiston vieressä.
Uuden automatisoidun tuotantolinjan keskiössä on konenäköjärjestelmä ja valvomohuone, josta prosessia voidaan valvoa menemättä robottien työalueelle. Linjan molemmissa päissä on järeät ABB IRB 8700 -robotit, jotka hoitavat anodilevyjen käsittelyn. Astetta pienempi ABB IRB 6700 -robotti vastaa levyjen kunnostamisesta ja rikkoutuneiden eristepalojen vaihdosta. Manuaalisten huoltotoimenpiteiden mahdollistamiseksi robotit toimivat erillisillä turva-alueilla. Yhden robotin työalueelle meneminen ei pysäytä koko prosessia.
Vaativaan ympäristöön valittiin robotit ABB:n kestävimmästä Foundry-tuoteluokasta.
”Projektin suunnitteluvaiheessa pohdittiin paljonkin robottien kokoluokkaa ja tahtiaikaa. Mallivalinnassa päädyttiin standardirobotteihin, jotka tarjoavat mahdollisimman laajan ja nopean varaosien ja huoltopalveluiden saatavuuden”, kertoo ABB:n myyntipäällikkö Jari Hyytiäinen.
Simulaatio helpottaa suunnittelua
Tuotannon tehokkuuden lisäksi uusi ratkaisu parantaa merkittävästi linjalla työskentelevän henkilöstön työhygieniaa ja -turvallisuutta.
”Aikaisemmin anodihuollosta vastaava työntekijä työskenteli avopisteessä ohjauspaneelin ääressä. Uuden automatisoidun laitteiston myötä prosessin valvonta hoituu valvomosta, ja tuotannon eri vaiheista poistuu merkittävä määrä käsityötä”, kertoo Boliden Kokkolan projekti-insinööri Pekka Tupeli.
Uusi laitteisto asennettiin jo aikaisemmin käytössä olleeseen tuotantotilaan, mikä asetti tiukat reunaehdot toteutukselle.
”Teimme paljon esityötä materiaalivirtojen suunnittelussa ja laitteiden sijoittelussa. ABB RobotStudio – simulaatiotyökalu oli tärkeä työkalu tässä vaiheessa”, Tupeli kertoo.
”Simulaation ja 3D-mallinnuksen ansiosta tuotantoprosessi pystyttiin suunnittelemaan hyvin pitkälti etukäteen”, kertoo Teemu Rantala Algolilta.
”Yhteistyö Bolidenin kanssa oli erittäin antoisaa, ja simulaatiovaiheessa saimme yhdessä toteutettua monia parannuksia kappaleiden käsittelyyn ja koko prosessin kulkuun.”
Konenäkö vie pidemmälle
Uusi automatisoitu laitteisto on tuotannollisessa koekäytössä, ja sen läpi ajetaan jo tehtaan normaalia päivätuotantoa. Bolidenille oli tärkeää saada mahdollisimman laaja säädettävyys tuotantoprosessin ja konenäköpohjaisen laadunvalvonnan parametreihin.
”Pystymme muokkaamaan hyvin tarkasti käsiteltävien anodilevyjen hylkäys- ja hyväksyntärajoja, ja jatkossa oma kunnossapitomme voi säätää järjestelmän asetuksia tarpeen mukaan”, Pekka Tupeli kertoo.
Uudet robotiikka- ja konenäkösovellukset mahdollistavat yhä useampien prosessin automatisoinnin, ja Bolidenin Kokkolan tehtaalla onkin jo käynnissä lukuisia uusia automatisointiprojekteja. Erityisesti 3D-konenäön avulla voidaan nykyään toteuttaa automatisoidusti monia sellaisia työvaiheita, jotka aiemmin olisivat edellyttäneet ihmissilmää ja
manuaalista päätöksentekoa.
”Perinteisten kokoonpanotehtävien lisäksi konenäköön tukeutuva automaatio tekee voimakkaasti tuloaan myös raskaaseen teollisuuteen. On kiinnostavaa havaita, että haasteet ja lainalaisuudet ovat oikeastaan aivan samanlaiset riippumatta siitä, mitataanko työkappaleen koko metreissä vai millimetreissä. Olennaista on se, miten robotiikkaa osataan hyödyntää uudella tavalla hankalien ja työläiden työvaiheiden automatisointiin ja tuotannon tehostamiseen”, kertoo Algol Technicsin Teemu Rantala.
**
Sinkkituotteiden elektrolyysiprosessin automatisointi
• 2 kpl ABB IRB 8700 -teollisuusrobotteja 4,2 m ulottumalla ja 550 kg hyötykuormalla
• 1 kpl ABB IRB 6700 -teollisuusrobotti 3,2 m ulottumalla ja 350 kg hyötykuormalla
• Siemens Simatic S7-1500 PLC-logiikka
• 31 kpl ABB ACS880 taajuusmuuttajia
• Cognex Vision -konenäköjärjestelmä 9 kameralla
• Ohjauspaneeli ja Siemens WinCC -käyttöliittymä valvomohuoneessa
• Turvatoiminnot robottien liikealueiden valvontaan